IKZ-HAUSTECHNIK, Ausgabe 03/2005, Seite 24 ff. SANITÄRTECHNIK |
Elektronische Gaslecksuche
Bernd Esders*
Die Gasinstallation ist ein Bereich mit hohen Sicherheitsanforderungen. Und das nur zu Recht, denn die Gefahren, beispielsweise durch ausströmendes Gas, sind allgemein bekannt. Aus diesen und weiteren Gründen trägt der Fachhandwerker eine große Verantwortung in der Gasinstallation. Für das Aufspüren von eventuellen Undichtigkeiten an Gasleitungen gibt es mittlerweile verschiedenste Möglichkeiten, angefangen von schaumbildenden Mitteln bis hin zu elektronischen Geräten mittels Sensortechnik.
Gemäß den technischen Regeln für Gas-Installationen (TRGI 86/96) ist unter Abschnitt 3.5.2 aufgeführt: "Undichtheiten an gasführenden Leitungen sind durch Gasspürgeräte oder mit schaumbildenden Mitteln nach DIN 30657 festzustellen."
Aufbau und Funktion von Sensorgeräten
Bei Gasspürgeräten kommen in der Regel Sensoren mit dem Wirkprinzip "Halbleiter" zum Einsatz. Vereinfacht dargestellt, besteht der Sensor aus einem Metalloxid, der zusammen mit einem Heizsystem in Keramik eingebettet ist. Das Heizsystem bringt den Sensor auf Betriebstemperatur, während das Metalloxid in der Umgebungsluft eine spezifische Leitfähigkeit annimmt. Bei Anwesenheit von brennbaren Gasen steigt die Leitfähigkeit des Sensors in Abhängigkeit von der Gaskonzentration. Ein wesentlicher Vorteil ist die schnelle Einsatzbereitschaft dieser Geräte nach durchschnittlich circa einer Minute, was dieses Messverfahren nicht zuletzt unkompliziert macht.
Bei der Großzahl der Geräte erfolgt der Betrieb im Diffusionsverfahren ohne Einsatz einer Pumpe. Der Halbleitersensor wird bei diesem Verfahren direkt an den zu prüfenden Leitungen und den Fittings vorbeigeführt. Hierfür ist das Gasspürgerät häufig mit einem abgesetzten Sensor am Kabel oder an einem Schwanenhals versehen. Gelangt Gas an den Sensor, wird der Anwender durch ein Tonsignal, Leuchtdioden, eine LCD-Anzeige oder neuerdings auch durch einen Vibrationsalarm informiert. Für ein effektives Arbeiten ist es jedoch vorteilhaft, wenn nicht ständig die Anzeige oder die Leuchtdioden beobachtet werden müssen.
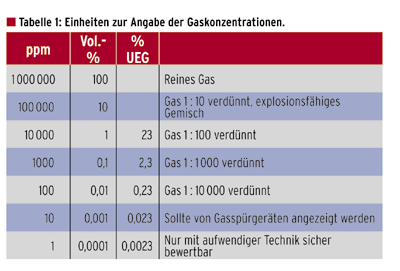
Die Anforderungen an Gasspürgeräte beschreibt die Deutsche Vereinigung des Gas- und Wasserfaches (DVGW) im Hinweis G 465-4 "Gasspür- und Gaskonzentrationsmessgeräte für die Überprüfung von Gasanlagen". Da Messgeräte mittlerweile Gas schon in geringsten Konzentrationen erkennen müssen, haben sich auch die Geräteanforderungen deutlich erhöht. Dabei werden Gaskonzentrationen in den Einheiten (Tabelle 1):
- ppm = part per million (Teile von einer Millionen Teile),
- % UEG = % der unteren Explosionsgrenze oder
- Vol.-% = Teile von 100 Teilen gemessen.
Praxiseinsatz
Zeit ist bekanntlich Geld, darum müssen Handwerksbetriebe und deren Mitarbeiter häufig unter Zeitdruck arbeiten. Jedoch verträgt sich extremer Zeitdruck nicht mit sicherem Arbeiten, insbesondere nicht bei der Sicherheitsbeurteilung einer Gasanlage. Darum können Gasspürgeräte in Hinsicht auf schnelles Arbeiten gar nicht empfindlich genug sein. Oder mit anderen Worten: Bei einer hohen Empfindlichkeit besteht die Möglichkeit, den Sensor mit "großer Geschwindigkeit" an den Leitungen sowie den Verbindungsteilen entlang zu führen, da bereits geringste Gasmengen ausreichen, um den Anwender zu alarmieren. Der Nachteil ist jedoch, dass auch bei "technisch dichten" Leitungen noch Gasanzeigen auftreten können, wenn der Sensor längere Zeit an eine Verbindungsstelle gehalten wird. Der Grund dafür: Bei Gasspürgeräten mit Diffusionskopf kann sich das leichtere Erdgas im Sensorkopf ansammeln. Entscheidend für diesen Vorgang ist neben der Verharrungszeit insbesondere der Abstand zwischen dem Sensorkopf und der Verbindungsstelle (Bilder 1 und 2).
Bild 1: Gasdiffusion am Sensorkopf bei einem Abstand von circa 1 - 2 cm. Nur ein Teilstrom des Gases gelangt in den Sensorkopf. |
Sollen nur Leckstellen geortet werden, deren Ortung auch Sinn macht, sprich, die instand gesetzt werden müssen, kann die Empfindlichkeit wesentlich niedriger liegen. In diesem Fall brauchte eine Alarmierung erst ab einigen 100 ppm einsetzen. Der Nachteil eines solchen Gerätes ist jedoch, dass die Empfindlichkeit nicht ausreicht, um Gas in der Raumluft anzuzeigen, bevor es bei einer Konzentration von etwa 200 - 300 ppm riechbar wird. Grundsätzlich ist es daher (siehe auch Ansprüche des DVGW Hinweises G 465-4) empfehlenswert, ein Messgerät mit hoher Auflösung (mindestens 10 ppm) und Empfindlichkeit einzusetzen. Damit erhält der Anwender einen Hinweis auf kleinste Gasspuren in der Umgebungsluft, sodass die Gasleitung zügig abgespürt werden kann.
Bild 2: Gasdiffusion bei einem unmittelbaren Kontakt des Sensorkopfes mit dem Fitting. |
Die anschließende Bewertung hängt stark von der Erfahrung des Monteurs ab. Eine eindeutige Bewertung ist letztendlich nur durch eine Gebrauchsfähigkeitsprüfung mittels einer Leckmengenmessung (Leckmengenmessgerät) und nicht durch ein reines Gasspürgerät möglich. Denn nur bei der Ermittlung der Leckrate in Liter pro Stunde für die gesamte Anlage (Gebrauchsfähigkeitsprüfung) kann, mittels der TRGI (Abschnitt 3.5.3 und 3.5.4), eine Klassifizierung der Gebrauchsfähigkeit durchgeführt werden.
Arbeitsablauf
- Gasspürgerät bereits außerhalb des Raumes mit der Gasinstallation einschalten und einlaufen lassen. Die Einlaufzeit nutzen, um das Gerät einer Sichtkontrolle zu unterziehen, wobei der Sensorkopf besonders auf Verschmutzung kontrolliert werden sollte.
- Beim Betreten des Raumes die Anzeige beobachten um durch eventuelle geringe Gasanzeigen in der Raumluft erste Hinweise auf Undichtheiten zu erhalten.
- Die Gasleitung (im direkten Kontakt) systematisch mit gleichbleibender Geschwindigkeit prüfen, die zur Wand gerichtete Seite nicht vernachlässigen und dabei auch auf Mängel wie Rost, fehlende Befestigungen, fehlerhafte Materialien usw. achten. Ein häufig gemachter Fehler ist es, nach dem Orten einer Leckstelle, nicht den gesamten weiteren Leitungsverlauf ebenfalls sorgfältig zu prüfen.
- Bei einer Gasanzeige die Position der Leckage möglichst genau feststellen und die höchste gemessene Konzentration dokumentieren. Anschließend in gleicher Position, aber mit circa 1 - 2 cm Abstand, erneut eine Messung durchführen. Wird in diesem Abstand nur noch eine sehr geringe Konzentration gemessen, so ist die Leckage anders zu bewerten, als bei weiterhin hohen Messwerten.
Beispiel: An einer Installationswand wurde eine künstliche Leckstelle an einer gehanften Gewindeverbindung erstellt. Über ein Leckmengenmessgerät betrug die Leckrate circa 0,6 l/h. An dieser Leckstelle wurden direkt am Fitting Konzentrationen von weit über 1 Vol.-% (10.000 ppm) gemessen. In 1-2 cm Abstand waren es noch mehr als 5000 ppm. Auch bei einer Reduzierung der Leckrate auf 0,1 l/h, wurde an der Leckstelle immer noch ein Wert von über 10.000 ppm gemessen. In geringem Abstand waren es jedoch weniger als 1000 ppm.
Bild 3: Gaskonzentration > 1 Vol. -% bei Messung direkt an der Leckage. |
Leider können für die Beurteilung der Vol.-%- bzw. der ppm-Werte keine Verbindlichen Angaben gemacht werden, da die Anzeigen auch von äußeren Umgebungsbedingungen beeinflusst werden. So wird sich beispielsweise die Situation in einem sehr gut belüfteten Raum mit starker Luftströmung anders darstellen, als in Bereichen mit geringen Luftströmungen.
Um eine Anlage beurteilen zu können, müssen neben den frei liegenden Gasleitungen auch die nicht sichtbaren Leitungsteile überprüft werden. Dies ist nur durch eine Gebrauchsfähigkeitsprüfung oder Druckprüfung erreichbar.
Verantwortung des Fachmanns
Wie eingangs beschrieben, obliegt dem SHK-Handwerker eine große Verantwortung im Zuge der Leckageprüfung. Daraus folgt auch, dass er bei diesen Arbeiten eventuell andere Mängel an der Gasanlage (insbesondere an der Leitungsanlage) aufdeckt und den Kunden entsprechend informiert. Eine derartige Betrachtung wird besonders beim "GasCheck" des SHK-Handwerks durchgeführt. Weiterhin muss, gemäß der Erläuterung zur TRGI, bei einem Gasgeruch in jedem Fall die Ursache beseitigt werden, unabhängig davon ob es sich um eine große oder kleine Leckage handelt.
Bild 4: Gaskonzentration nur 300 ppm (0,03 Vol.-%) bei Messung im Abstand von circa 1 cm. |
Ein abschließender Hinweis: Die Sensoren der Gasspürgeräte können durch eine Reihe von Substanzen (beispielsweise durch Silikondämpfe) beeinträchtigt werden. Um einen derartigen Empfindlichkeitsverlust auszuschließen, ist es notwendig eine regelmäßige Überprüfung der Anzeigeempfindlichkeit mittels Prüfgas vorzunehmen. Mit einer Druckgasdose kann der SHK-Handwerker diese Überprüfung selbst durchführen.
Internetinformationen: |
B i l d e r : Esders Ingenieurbüro GmbH
* Bernd Esders, Esders Ingenieurbüro GmbH, Haselünne
[Zurück] [Übersicht] [www.ikz.de]