IKZ-HAUSTECHNIK, Ausgabe 2/1998, Seite 72 ff.
REPORT
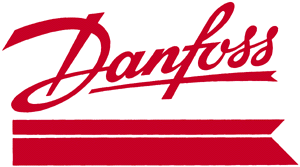
Mit Qualitätssicherung zur Nr. 1
Aus einer kleinen Firma, deren Grundstein Mads Clausen 1933 in Dänemark legte, entwickelte sich im Laufe der Zeit ein Unternehmen mit heute 18000 Beschäftigten auf der ganzen Welt. IKZ-HAUSTECHNIK-Redakteur Detlev Knecht hatte die Gelegenheit, drei Werke in Dänemark zu besichtigen: die Produktionsstätte für Öldüsen und die Werke für Heizkörperthermostatventilgehäuse und Fühlerelemente.
Danfoss als Unternehmen
Im Jahre 1985 wurde Danfoss als eines der ersten Unternehmen der Branche von der British Standards Institution in Übereinstimmung mit BS 5750, Teil 1, zertifiziert und bereits 1989 erhielt das Unternehmen das ISO 9001-Zertifikat. Damit unterstreicht das dänische Unternehmen den hohen Stellenwert, den die hohe Qualitätsgüte von Produkten und Dienstleistungen einnimmt. Wie ein roter Faden zieht sie sich durch alle Abteilungen: von der Produktplanung bis zur Materialbeschaffung, von der Marketingabteilung bis zum Kundendienst, von der Arbeitsvorbereitung bis zur Endkontrolle.
Eine Öldüse besteht aus dem in dieser Darstellung sichtbaren Ölfilter, dem Düsenkörper (Gehäuse) und der Düsenplatte mit der Bohrung. Im Innern befinden sich der Düsenkegel und die Bodenschraube. |
Besonders wird auch die volle Zufriedenheit des Kunden und die Nähe zu ihm großgeschrieben. Danfoss-Gesellschaften bestehen in 37 Ländern der Erde, und zwar mit Geschäftsführungen und Belegschaften, die sich aus den Staatsangehörigen der Nationen zusammensetzen. Damit paßt sich Danfoss der Mentalität und der Kultur jedes einzelnen Landes an und verlangt nicht von seinen Kunden eine Anpassungsfähigkeit, die nie so weit reichen würde. In rund 70 weiteren Ländern ist Danfoss durch Vertragshändler vertreten, die Danfoss-Produkte auf Lager halten und vertreiben. Schließlich rundet das international tätige Unternehmen sein Engagement für die Kunden mit einem Netz von Service-Centern auf allen sechs Kontinenten ab. In Deutschland selbst beschäftigt Danfoss rund 3000 Mitarbeiter.
Zwei der fünf Bestandteile einer Öldüse: unten der Düsenkegel (mit Tangentialschlitzen), oben die Düsenplatte. |
Brennerkomponenten
Danfoss ist das weltweit führende Unternehmen im Bereich der Brennerkomponenten. Die Produktpalette umfaßt Regler, Ölpumpen, Ölvorwärmer, Thermostate, Zündeinrichtungen und Öldüsen. Auf dem Brennermarkt gibt es bis auf sehr wenige Brennerhersteller niemanden, der keine Danfoss-Bauteile verwendet.
Jede Düse wird elektronisch und visuell auf ihre einwandfreie Funktion hin überprüft. |
Öldüsenproduktion in Nordborg
Danfoss ist einer der wenigen Hersteller von Öldüsen, der außerhalb der USA produziert. Anläßlich der letzten ISH wurde die Produktion der einhundertmillionsten (!) Düse gefeiert. Dabei ist schon erstaunlich, mit welch einer Präzision eine Öldüse hergestellt wird, für die selbst ein Endkunde weniger als 20 Mark zu zahlen hat. Eine Öldüse besteht aus den fünf Bestandteilen Düsenkörper, Filter, Bodenschraube, Düsenkegel und Düsenplatte. Die Konstruktion und Bearbeitung der beiden zuletzt genannten Bauteile sind entscheidend für den Öldurchsatz, den Zerstäubungswinkel und das Zerstäubungsmuster.
Die zwei wichtigsten Bauteile einer Düse sind der Düsenkegel mit den Tangentialschlitzen sowie die Düsenplatte aus Edelstahl mit der Bohrung, aus der das Heizöl austritt. Die kleinste Bohrung hat einen Durchmesser von nur 0,15 mm (ein menschliches Barthaar ist im Durchmesser etwa gleich). Selbst der dafür verwendete kleine Bohrer mit einer Arbeitslänge von etwa 3 mm weist die typischen Schneidwendeln auf. Das bloße menschliche Auge vermag dies nicht mehr zu erkennen.
Praktisches Format - hilfreicher Inhalt: Das "Servicehandbuch" mit den Austauschmöglichkeiten von Brennerkomponenten. |
Die erwähnte Bohrung in der Düsenplatte ist nicht nur ein zylindrisches Loch, sondern weist auf der Einlauf- und Auslaufseite des Heizöls unterschiedliche Formen auf. Durch ein Fließpreßverfahren mit Werkzeugen aus spezialgehärtetem Edelstahl werden die trichterförmigen Konturen auf beiden Seiten hergestellt. Sie bestimmen das Zerstäubungsmuster und den Zerstäubungswinkel.
Stichwort Qualitätskontrolle: Schon während der Produktion werden stichprobenartig die fünf Düseneinzelteile auf Einhaltung der Toleranzgrenzen überprüft. In den drei folgenden Stufen des Zusammenbaus wird dann jeder Schritt sofort durch automatische Meßeinrichtungen überprüft. Mit dieser Maßnahme ist aber die Qualitätskontrolle noch nicht beendet. Sind alle Düsenbestandteile montiert, wird jede einzelne Öldüse, bevor sie die Produktion verläßt, auf Öldurchsatz, Zerstäubungswinkel und Zerstäubungsbild elektronisch und visuell überprüft. Dadurch gleicht in Funktion und Durchsatz eine Düse der anderen.
Diese Ausführungen belegen, daß das Brenner-Know-how in der Düse steckt, nicht in der Ölpumpe, im Zündtrafo o.ä. Denn der Toleranzbereich einer Düse, so melden die Verantwortlichen in Nordborg, liegt in engeren Grenzen als bei dem Innenleben einer Armbanduhr.
Dichtigkeitsprüfung von Ventilgehäusen. |
Servicehandbuch der Brennerkomponenten
Wenn es an der Zeit ist, Komponenten eines Ölbrenners auszutauschen, wird deutlich, wie komplex heutige Systeme aufgebaut sind. Danfoss hat deshalb vor kurzem ein Servicehandbuch herausgegeben, das die Arbeit des Kundendienstlers hilfreich unterstützt. Nach Baugruppen gegliedert informiert die Broschüre über den Austausch von Ölpumpen, Feuerungsautomaten, Zündeinheiten, Öldüsen und Ölvorwärmern verschiedener Hersteller. Das knapp 80 Seiten dicke Heftchen im DIN A6-Format gibt Danfoss kostenlos ab. Wie zu erfahren war, wird dieses neue Hilfsmittel vom Handwerker ausgesprochen positiv aufgenommen.
Computergesteuerte Formung der Wellrohre. |
Thermostatventilgehäuse-Produktion
Im dänischen Viby sorgen vier Schmiedepressen für Messingteile dafür, daß die Nachfrage nach Danfoss-Thermostatventilgehäusen und Verschraubungen gedeckt wird. 300 Mitarbeiter produzieren in drei Schichten alle Gehäuse sowie rund 700 weitere Produkte aus Hartmetall. Die Ventilgehäuse werden bei einer Temperatur von 700C mit 40 t Preßdruck in ihre Form gebracht. Nach Entgratung und luftgestützter Kühlung kommen sie in die halbautomatische Galvanisiererei, wo sie vernickelt werden.
Nach acht weiteren Bearbeitungsschritten, bei denen Bohrungen und Ausfräsungen hergestellt werden, erfolgt die erste Maßkontrolle. Kontinuierlich werden Ventilgehäuse der laufenden Produktion entnommen und in 34 Kontrollschritten auf Maßtoleranzen überprüft. Stellt sich dabei eine inakzeptable Differenz heraus, werden sämtliche Gehäuse einer Charge überprüft. Jedes der weiterlaufenden Ventilgehäuse wird außerdem visuell auf ordnungsgemäße Verarbeitung überprüft.
Der Zusammenbau der Einzelteile zu einem funktionstüchtigen Ventil geschieht vollautomatisch. Das Besondere dabei ist, daß jeder Bearbeitungsschritt (wie auch bei der Öldüsenproduktion) auf ordnungsgemäße Ausführung hin automatisch mit Hilfe von optischen Geräten überprüft wird. Auch hieran läßt sich erkennen, daß die Qualitätskontrolle aller Produkte großgeschrieben wird.
Laserschweißung des 0,8 mm dicken Kapillarrohres. |
Fühlerelemente-Produktion
Danfoss ist nicht nur der weltweit größte Hersteller von Thermostatventilgehäusen, sondern auch der weltweit größte Produzent von Thermostatventilköpfen, auch Fühlerelemente genannt. Außerdem ist Danfoss der einzige europäische Thermostatventilanbieter, der die Wellrohre, Herzstück eines jeden Thermostaten, selbst herstellt.
Dies geschieht in Silkeborg: Aus einem etwa 35 mm breiten Zinnbronze-Band werden "Münzen" herausgestanzt, die im weiteren Produktionsschritt zu einer Hülse (ähnlich einem kleinen Reagenzglas) mit einer Wanddicke von 0,1 mm gezogen werden. Danach gelangt die Hülse in eine Preßmaschine, die daraus das besagte Wellrohr herstellt. Weil Danfoss besonderen Wert auf hohe Produktionsqualität legt, wird das Wellrohr sofort auf Dichtheit überprüft. Ist alles in Ordnung, folgen die weiteren Produktionsschritte.
Montageautomat für RA 2000 Fühlerelemente. |
Am Beispiel des gasgefüllten Wellrohrelements soll der weitere Produktionsablauf beschrieben werden. Nachdem das Wellrohr mit der Kapsel im Laserverfahren verschweißt wurde, folgt der Füllvorgang. Bevor jedoch das Wellrohr mit dem Gas gefüllt wird, wird es auf mechanische Eigenschaften hin exakt gemessen. Denn die bei der Produktion zwangsläufig auftretenden Fertigungstoleranzen würden große Unterschiede im Regelverhalten ergeben, würden alle Elemente pauschal mit dem gleichen Zweistoffgas gefüllt. Nach der besagten Messung berechnet ein Computer die individuelle Gaszusammensetzung und den notwendigen Gasfülldruck. Nachdem der Fühler mit beiden Gasen gefüllt wurde, erfolgt sofort die Kontrolle des Kopfes. Jeder Fühler wird auf exakt 50C erwärmt, während ein Meßcomputer den Ausdehnungsdruck der Kapsel auf Einhaltung des Solldruckes überprüft. So ist sichergestellt, daß jeder Fühler beim Kunden die Aufgabe erfüllt, die ihm zugeteilt ist, nämlich die Regelung der Raumtemperatur.
In jedem Danfoss-Thermostatventil (Unter- und Oberteil) stecken über 70 Patente. Die einen beziehen sich auf die Art und Weise der Herstellung, die anderen auf Details des Thermostaten selbst. Der vor rund fünf Jahren eingeführte Schnappverschluß beispielsweise gehört dazu.
Zukünftiges
Wirtschaftliches Wachstum und Umweltbewußtsein - zwei Aufgaben, die sich aus der Sicht von Danfoss nicht ausschließen. Auch deshalb fühlt sich das dänische Unternehmen verpflichtet, das Leistungsvermögen seiner Industrieanlagen weiter zu steigern und gleichzeitig den Energieverbrauch zu senken. Ziele, die einen Großteil der Aktivitäten von Danfoss in den nächsten Jahren bestimmen werden.
[Zurück] [Übersicht] [www.ikz.de]